This form is the fastest way to contact us for a free consultation, quote and price list request, we will reply you asap.
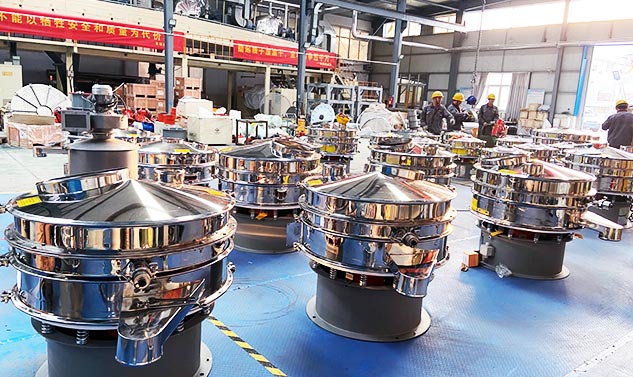
- Whatsapp: +86 134 6222 7588
- Wechat: +86 134 6222 7588
- E-Mail:sales@dzscreen.com
- Skype: +86 134 6222 7588
In today’s industrial landscape, optimizing material handling is key to staying competitive. A vibrating feeder might not grab headlines, but its ability to streamline operations makes it a vital asset in countless industries. This article explores what makes vibrating feeders essential, their standout features, practical applications, and tips for maximizing their value—all tailored to help your B2B business thrive.
A vibrating feeder is a specialized piece of industrial equipment that uses vibrations to move bulk materials—think gravel, powders, or small components—from one point to another. Typically integrated into production lines, it ensures a consistent, controlled flow of materials to downstream processes.
Vibration Source: Powered by an electromagnetic or mechanical drive, it generates steady oscillations.
Material Transport: These vibrations propel materials along a tray or chute.
Adjustability: Operators can tweak the vibration frequency to fine-tune the flow rate.
This straightforward design delivers reliable material feeding with minimal fuss.
Here’s why vibrating feeders are a game-changer for businesses:
Steady Output: They maintain an even flow, reducing bottlenecks in production.
Low Maintenance: Simple construction means fewer breakdowns and less downtime.
Versatility: Suitable for everything from sticky powders to abrasive rocks.
Cost Savings: Automation cuts labor costs and boosts throughput.
Compact Design: Fits seamlessly into tight spaces on the factory floor.
These qualities make vibrating feeders a go-to for automated material handling systems.
Vibrating feeders prove their worth across diverse sectors:
Mining: Moving ore or coal to crushers with unwavering consistency.
Food Processing: Gently feeding grains or spices without clumping.
Construction: Delivering aggregates to batching plants efficiently.
Take a U.S.-based quarry: after adopting a vibrating feeder, they cut material jams by 30%, proving its knack for smoothing out workflows.
Choosing the right feeder isn’t one-size-fits-all. Consider these factors:
Material Type: Match the feeder to your material’s weight, texture, and moisture level.
Throughput Needs: Ensure it meets your production volume demands.
Durability: Opt for corrosion-resistant finishes if handling harsh substances.
Power Options: Electromagnetic for precision, mechanical for heavy-duty tasks.
Supplier Expertise: Partner with vendors offering solid technical support.
A smart choice turns your feeder into a tailored efficiency booster.
Maximize uptime with these tips:
Routine Checks: Inspect for loose bolts or worn parts monthly.
Cleanliness: Remove debris to prevent blockages.
Vibration Tuning: Recalibrate periodically for optimal flow.
Spare Parts: Stock key components to avoid delays.
Good care keeps your feeder a trustworthy workhorse.
The technology isn’t standing still. Watch for:
Smart Controls: Sensors to adjust flow based on real-time demand.
Eco-Friendly Designs: Lower energy use with efficient motors.
Modular Builds: Quick swaps for parts or upgrades.
Specialized Models: Feeders built for ultra-fine or hazardous materials.
These trends signal a future where vibrating feeders play an even bigger role in cutting-edge material handling.
Vibrating feeders quietly revolutionize how materials move through your facility. They save time, cut costs, and keep production humming—perfect for any business aiming to scale. Ready to see the difference? Check out our vibrating feeder lineup and let’s find the right fit for your needs.
This form is the fastest way to contact us for a free consultation, quote and price list request, we will reply you asap.
Copyright © 2012-2023 Xinxiang Dongzhen Machinery Co., Ltd. All Rights Reserved.